PFAS-free polymer membranes for semiconductor processing
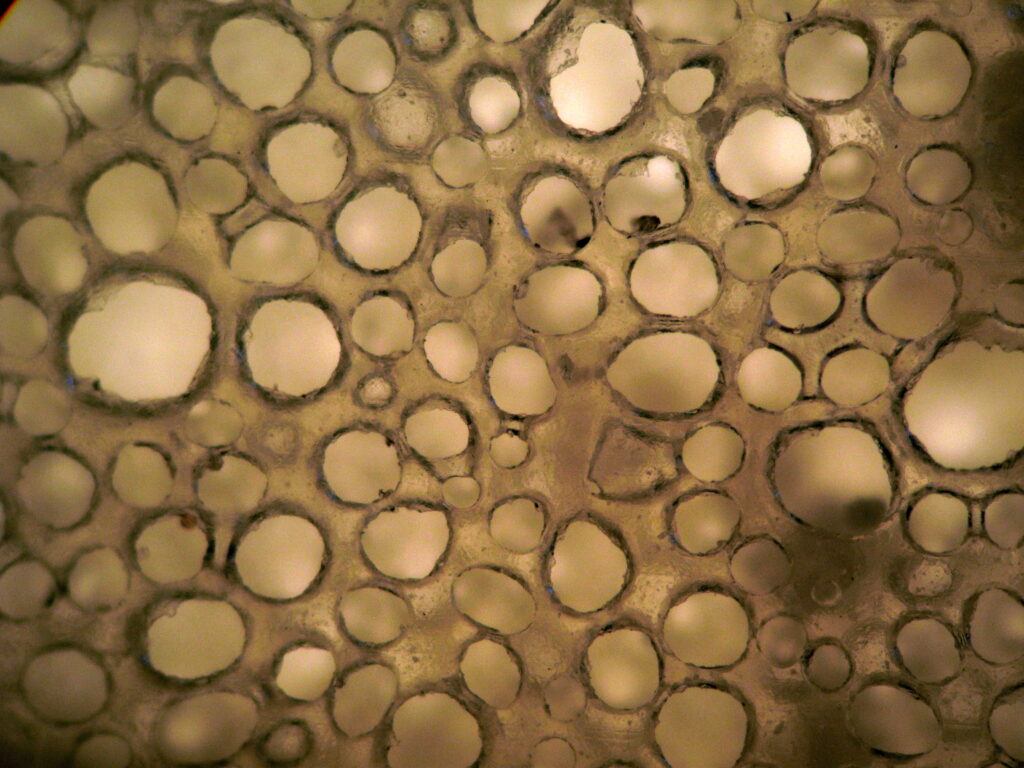
Image: Wikimedia Commons
PFAS chemicals are toxic. They contaminate water and soil and accumulate in humans and animals via food and consumer goods. The European Chemicals Agency (ECHA) therefore published a proposal in February 2023 that would ban the production, use and distribution (including import) of PFAS in the European Economic Area. The semiconductor industry views the impending PFAS ban as a critical issue, as the chemicals are used as membranes and housings in filters as well as in processes such as etching and cleaning. According to many manufacturers, there is no viable alternative to sustainable per- and polyfluoroalkyl chemicals. A ban would make the production of most semiconductor products impossible.
PFAS-free membrane
Researchers at the Fraunhofer IAP in Potsdam have now succeeded in developing a PFAS-free membrane for a supplier to the semiconductor industry. This membrane is based on conventional, specially stabilized polymers. It could replace PFAS membranes. The polymer polyacrylonitrile membrane (PAN) offers a high degree of chemical and mechanical stability. It also has an extremely small pore diameter of around seven nanometers. This is necessary to separate particulate impurities from the production process and to filter and recycle the liquids required for the process, such as acids and solvents. The membrane can be adapted to specific requirements. As a result, this new application can be easily integrated into existing systems to produce the next generation of chips.
Avoiding impurities and contamination
“The production of chips involves numerous process steps such as cutting, cleaning and smoothing in order to apply the structures to the wafer. All of these processes generate particulate contaminants that must be separated during each process, otherwise they would impair the formation of nanometer-sized structures,” says Dr. Murat Tutus, engineer at the Fraunhofer IAP and head of the ‘Membranes and Functional Films’ department. Murat Tutus and his team have succeeded in producing a chemically and mechanically very stable membrane from conventional polymer. This membrane can filter particles with a pore size of just seven nanometers. By comparison, filters with a pore size of 220 nanometers are used for sterile filtration in medical technology. “With another component we developed, we were able to chemically modify the polymer and stabilize it even under harsh conditions,” says the researcher.
Degree of permeability of the membrane window
The researchers’ task was also to achieve a pore size distribution that deviated only insignificantly from seven nanometers. In addition, the membrane must be very permeable. “The degree of permeability is determined by the number of pores on the surface.” The smaller the pores, the lower the permeability. In order to increase the permeability, we therefore had to increase the number of pores in a second step while keeping the pore size constant,” explains Tutus.
Membrane production with REACH-compliant solvents
As the pore size and permeability of the membrane can be adjusted to specific requirements, it is easy to adapt it to different applications in other industries. Another advantage of membrane customization is that existing systems can be used and no training of personnel is required. DR. Tutus and his team see great potential for their developments in the pharmaceutical and chemical industries, where aggressive solvents are also used. The membrane production itself uses REACH-compliant solvents (Registration, Evaluation, Authorization and Restriction of Chemicals) and low temperatures throughout, making it a sustainable process overall. The membrane is produced using a NIPS (non-solvent-induced phase separation) process, which also allows researchers to customize the morphology or pressure stability of the membrane.
Source: Fraunoffer
Also read: How mid-sized companies are preparing for the PFAS ban
Reservation
This information has been compiled with the greatest possible care, in some cases from different information sources. (Interpretation) errors are not excluded. No legal obligation can therefore be derived from this text. Everyone dealing with this subject has the responsibility to delve into the matter!